Unveiling the Magic of Diced Silicon Wafers with Dry Oxide Coating: The Prime-Grade 4-Inch Silicon W
- Kelly Clifford
- Jun 8, 2023
- 2 min read
Introduction:
In the realm of semiconductor technology, silicon wafers are the building blocks that enable the production of integrated circuits and electronic devices. These wafers undergo various processes and enhancements to meet the stringent requirements of the industry. In this blog post, we will explore the fascinating world of diced silicon wafers with a dry oxide coating, focusing on prime-grade 4-inch silicon wafers and their significance in semiconductor manufacturing.
Understanding Diced Silicon Wafers with Dry Oxide Coating:
Diced silicon wafer with a dry oxide coating refers to the process of cutting a single large silicon wafer into smaller individual pieces or dies. Each diced wafer serves as a substrate for the fabrication of individual electronic components. To enhance the performance and reliability of these diced wafers, a dry oxide coating is often applied.
The dry oxide coating is a thin layer of silicon dioxide (SiO2) that is thermally grown on the surface of the diced silicon wafers. This oxide layer provides a protective barrier, preventing contamination, reducing surface defects, and improving the electrical insulation properties of the wafer.
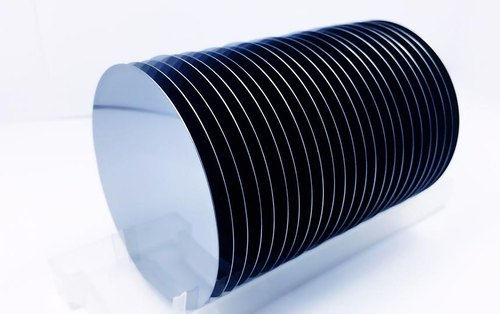
Prime-Grade 4-Inch Silicon Wafers:
Prime-grade 4-inch silicon wafers are considered high-quality substrates widely used in semiconductor manufacturing. The term "prime grade" signifies the highest level of purity and quality among silicon wafers. These wafers undergo a stringent selection process to ensure minimal defects, uniform thickness, and superior crystal structure.
Applications and Benefits of Diced Silicon Wafers with Dry Oxide Coating:
Integrated Circuit Fabrication: Diced silicon wafers with a dry oxide coating are fundamental in the production of integrated circuits. The diced wafers serve as the foundation for the deposition of various layers, including semiconductors, metals, and dielectrics, enabling the creation of intricate circuitry. The dry oxide coating acts as an insulating layer, preventing leakage currents and improving the reliability of the fabricated circuits.
MEMS (Micro-Electro-Mechanical Systems): Micro-electro-mechanical systems, commonly known as MEMS, are miniature devices that combine mechanical and electrical components on a single chip. Diced silicon wafers with a dry oxide coating are essential in the fabrication of MEMS devices, as they provide a stable and reliable substrate for the deposition and integration of mechanical and electrical elements.
Comments